PROFILO DI RISCHIO NEL COMPARTO: FILATURA DEL CARDATO
1. COMPARTO : FILATURA DEL CARDATO NELL'AREA PRATESE
2. CODICI ISTAT : 17.12
3. CODICE ISPESL :
ZONA DI RILEVAZIONE
4. NAZIONALE :
5. REGIONALE :
6. PROVINCIALE : PRATO - PISTOIA - FIRENZE
7. USL : N.9 PRATO - N.8 PISTOIA - N.10 FIRENZE
8. ANNO RILEVAZIONE : 1995
9. NUMERO ADDETTI
9A. IMPIEGATI : 4894 (*) uomini
9B. OPERAI :
10. N.AZIENDE : 431 (*)
11. STRUTTURA DI RILEVAZIONE : ARPAT - SETTORE TECNICO CEDIF
VIA BARACCA,9 - 50127 FIRENZE
12. REFERENTE
QUALIFICA :
NOME : STEFANO
COGNOME : BECCASTRINI
INDIRIZZO : VIA BARACCA, 9
CAP : 50127
CITTÀ : FIRENZE
PROVINCIA : FI
TELEFONO : 055/32061 - 055/3206357
FAX : 055/3206367
E-MAIL : g.banchi@arpat.toscana.it
13. INFORTUNI: TOTALE 301 (**) DI CUI MORTALI 0
14. MALATTIE PROFESSIONALI
DENOMINAZIONE |
N.CASI |
COD.INAIL |
IPOACUSIE DA RUMORE |
|
|
|
|
|
|
|
|
|
|
|
|
|
|
|
|
|
|
|
|
|
|
|
NOTE:
(*) dati riferiti all'anno 1992
(**) infortuni rilevati su un campione di 352 aziende di Filatura del Cardato nel territorio della ASL n.9 di Prato, nell'anno 1992
Capitolo 1
GENERALITA' SUL COMPARTO FILATURA
NELL'AREA PRATESE
1- GENERALITA'
L'industria tessile ha una serie di processi lavorativi finalizzati al trattamento delle fibre per la produzione di tessuti di vario tipo e di diverse qualità.
In Toscana questa industria è particolarmente sviluppata in un'area, detta del pratese, che comprende la provincia di Prato e le zone limitrofe delle province di Pistoia e Firenze.
L'asse portante delle aziende tessili presenti in questa area è costituito dal comparto della filatura del cardato, che occupa circa il 10% degli addetti del settore e che a livello nazionale produce circa il 60% del totale dei fusi di filatura.
Il comparto "filatura" nell’area pratese, comprende varie tipologie di aziende, la cui attività prevalente può essere identificata come segue:
- filatura del cardato: vengono generalmente utilizzate fibre corte, che possono essere naturali o rigenerate; nel passato la lavorazione del cardato tipicamente pratese è stata caratterizzata soprattutto da un largo uso di fibre rigenerate provenienti dagli stracci.
- filatura a pettine: vengono generalmente utilizzate fibre lunghe e costituisce una lavorazione che produce filati di alta qualità.
- filatura open-end: prende il nome dal tipo di macchina utilizzata per la filatura e costituisce una lavorazione che produce filati di alta qualità.
- strappo delle fibre sintetiche: queste industrie si occupano della preparazione del nastro pettinato da avviare alla filatura a pettine.
Numero delle aziende di filatura del cardato nell'area pratese censite dai servizi PISLL.
Dati aggiornati al 1992:
|
Filatura
del cardato |
|
numero aziende |
numero addetti |
AUSL 9
Prato |
376 |
4140
|
AUSL 10 (ex G) Sesto F.no |
28 |
368
|
AUSL 8
Pistoia |
27 |
386
|
Dall'analisi dei dati, considerando che le lavorazioni vengono svolte su almeno due turni di lavoro, risulta anche la presenza di piccole aziende che impiegano solo cinque addetti per turno.
L'incidenza degli infortuni nella filatura del cardato è da sempre elevata , non solo per la numerosità, ma anche e soprattutto per la gravità degli incidenti, che molto spesso comportano invalidità permanente.
Andamento del fenomeno infortunistico in un campione di 352 aziende di filatura del cardato della USL 9 di Prato
ANNO |
1988 |
1989 |
1990 |
1991 |
1992 |
numero di addetti |
3673 |
3746 |
3736 |
3678 |
3892 |
infortuni vari (*) |
143 |
161 |
148 |
183 |
183 |
infortuni 1-8 giorni |
17 |
12 |
18 |
17 |
23 |
infortuni 9-30 giorni |
41 |
51 |
54 |
45 |
56 |
infortuni > 30 giorni |
26 |
43 |
34 |
25 |
24 |
infortuni totali |
227 |
267 |
254 |
270 |
301 |
(*) infortuni non causati da mancanza di protezioni sulle macchine
L'intervento del servizio PISLL di Prato, che ha effettuato nell'anno 1987 un piano mirato di prevenzione, ha portato ad una diminuzione degli infortuni più gravi, come è anche evidenziato dalla tabella sopra riportata.
Tale obbiettivo è stato realizzato anche per mezzo del già citato protocollo di intesa tra le parti sociali, che ha mirato soprattutto ad impartire prescrizioni sull'applicazione della normativa ed a dare indicazioni sulle modalità di effettuazione delle operazioni. e sull'organizzazione del lavoro.
In questo quaderno sul profilo di rischio e le soluzioni della filatura del cardato vengono riportate le misure di sicurezza individuate in quel protocollo e nelle esperienze successive.
Il fenomeno infortunistico nelle altre tipologie di aziende del comparto filatura è meno significativo.
Capitolo 2
DESCRIZIONE GENERALE DEL CICLO LAVORATIVO
e
SCHEMI A BLOCCHI
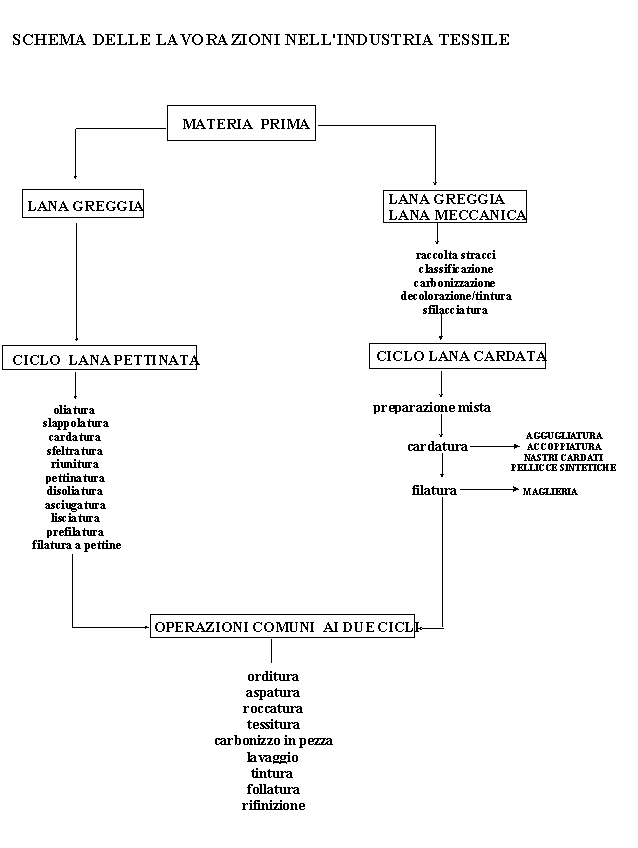
SCHEMA GENERALE DEL CICLO DI FILATURA NELL’AREA PRATESE
SCHEMA DEL PROCESSO DI FILATURA A CARDATO NELL’AREA PRATESE
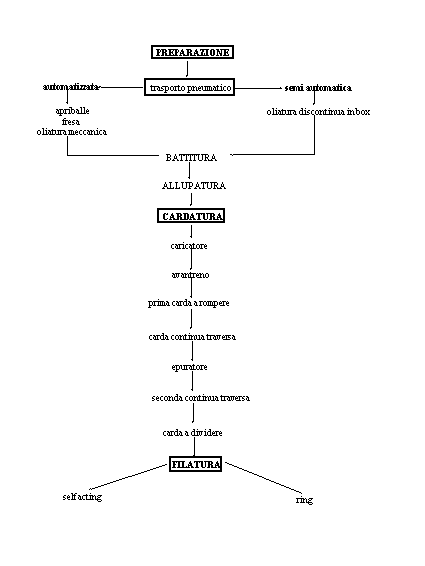
SCHEMA DEL PROCESSO DI STRAPPO FIBRE SINTETICHE NELL’AREA PRATESE
SCHEMA DEL PROCESSO DI FILATURA A PETTINE NELL’AREA PRATESE
SCHEMA DEL PROCESSO DI FILATURA OPEN-END NELL’AREA PRATESE
Capitolo 3
ANALISI DEI RISCHI, DANNI E SOLUZIONI
3.1 ANALISI DEI RISCHI, DANNI E SOLUZIONI nelle attività di "FILATURA DEL CARDATO"
- ANALISI RISCHI, DANNI E SOLUZIONI nella fase "PREPARAZIONE DELLA MISTA"
1. FASE DI LAVORAZIONE : PREPARAZIONE DELLA MISTA
2. COD.INAIL :
3. FATTORE DI RISCHIO : Rischi per la salute e igienico ambientali:
esposizione a polveri (fibre tessili);
esposizione a rumore.
Rischi per la sicurezza:
carenza di sicurezza su macchine (lavoro in prossimità di organi meccanici in movimento);
manipolazione di sostanze pericolose (oleanti);
incendio;
carenza di sicurezza elettrica.
4. CODICE DI RISCHIO :
5. N.ADDETTI :
3.1.1.1 DESCRIZIONE DELLA FASE "PREPARAZIONE DELLA MISTA"
Questa fase serve a miscelare al meglio le materie prime e ad effettuare una prima apertura delle fibre già trattate nella rigenerazione; di conseguenza si ottiene anche la miscelazione di materiali di colori diversi per avere colorazioni intermedie.
Durante questa operazione il materiale viene introdotto nella macchina battitora previa impregnatura con liquidi oleosi, in quantità variabili dall' 8 al 15% del peso delle fibre; tali sostanze, costituite per lo più da tensioattivi e glicoli, hanno la funzione di facilitare la coesione delle fibre al fine di ottenere come prodotto finale uno stoppino omogeneo e resistente.
La battitora effettua una separazione dei corpi estranei dalle fibre corte; successivamente un impianto pneumatico trasferisce il tutto alla lupa che esegue l'apertura delle fibre che vengono poi depositate in box dai quali sono immesse nel ciclo di cardatura. Un tempo, ed in alcuni impianti ancora oggi, le operazioni di prima miscelazione delle fibre venivano svolte manualmente dagli "allupini", e la successiva oliatura avveniva tramite cicloni direttamente nei locali di lavorazione. Negli impianti moderni le fasi di apertura dei colli e di prima miscelazione vengono effettuate per mezzo di macchine apriballe e di frese automatiche nelle camere di mista e l'oliatura tramite oliatori automatici chiusi.
3.1.1.2 ATTREZZATURE E MACCHINE NELLA FASE "PREPARAZIONE DELLA MISTA"
- Macchina apriballe: E' costituita da un nastro trasportatore, sul quale vengono appoggiati i colli delle materie prime liberati dall'imballo, che avanza lentamente per alcuni metri. fino ad un'impannata provvista di aculei metallici, con movimento quasi verticale che ha la funzione di asportare le fibre dai colli, favorendone la miscelazione ed una prima apertura. Dall'impannata trasportatori meccanici o pneumatici provvedono ad inviare in appositi box o "camere e di mista" il materiale.
- Camera di mista e di fresa: In tali camere avviene l'immagazzinamento temporaneo e la stratificazione delle fibre provenienti dall'apriballe per consentire un'alimentazione omogenea per composizione e per colore delle altre macchine della preparazione. La camera di mista è formata da un box in cui una parete è sostituita da una fresa mobile che a sua volta è costituita da un'impannata a movimento verticale, provvista di aculei, che scorre lentamente su apposite guide poste sul pavimento e si inserisce all'interno della camera di mista prelevando il materiale in essa stratificato. La parete superiore generalmente è fornita di aperture per la fuoriuscita dell'aria proveniente dall'impianto di trasporto pneumatico del materiale in lavorazione.
- Battitora: Questa macchina ha lo scopo di battere le fibre per far cadere le impurità e al contempo procedere all'apertura delle stesse. La macchina è costituita dalle seguenti parti:
- alimentazione manuale, meccanica o pneumatica
- tamburo o aspo munito di punte meccaniche
- moscaiola o scarta bottoni
- zona con portelli per la rimozione del materiale in eccesso
- zona di uscita
- Lupa: Questa macchina ha lo scopo di aprire, depurare e miscelare le fibre prima della cardatura ed è costituita dalle seguenti parti:
- la zona di alimentazione, che può essere manuale, meccanica o pneumatica, costituita da un nastro trasportatore o impannata.
- gli ingollini.
- la botte chiodata.
- la moscaiola.
- la zona di uscita.
- Carda Lupo: questa macchina, essendo provvista anche di gruppi cardanti non presenti nella lupa, viene usata per aprire meglio la massa delle fibre.
Essa comprende:
- l'alimentazione, generalmente pneumatica, che è costituita dal nastro trasportatore, dai cilindri alimentatori o ingollini e dal rubano.
- la zona cardante costituita dal gran tamburo, ricoperto da guarnizioni metalliche con punte rigide, sovrastato da diverse coppie cardanti e da cilindri lavoratori e spogliatori, anch'essi muniti di guarnizioni metalliche a punte rigide.
- la zona di uscita costituita dal volano, che è un cilindro munito di guarnizioni metalliche con punte lunghe e flessibili che distacca le fibre, dal gran tamburo e dal nastro di uscita che raccoglie il materiale lavorato da inviare poi tramite l'impianto pneumatico alle fasi successive di lavorazione.
- Impianto chiuso di oliatura: Questa macchina è presente negli impianti più moderni in sostituzione dei box di mista e oliatura semiautomatica o manuale. E' costituita da una camera cilindrica verticale all'interno della quale, nella parte inferiore, si trova un piatto ruotante sovrastato dagli ugelli che spruzzano la sostanza oleante. Il materiale in lavorazione viene introdotto dall'alto, riceve l'oleante e forma uno strato sottile sul piatto che ne arresta la caduta e successivamente viene prelevato ed inviato all'impianto di cardatura. Uno sportello apribile, munito di un oblò trasparente, consente di verificare il funzionamento.
- Impianto di trasporto pneumatico: L'impianto ha lo scopo di movimentare il materiale in lavorazione ed alimentare e scaricare le varie macchine.
3.1.1.3 FATTORI DI RISCHIO, FASE "PREPARAZIONE DELLA MISTA"
In questo reparto i principali fattori di rischio sono i seguenti:
- Lavoro in prossimità di organi meccanici in movimento, costituiti dagli organi lavoratori delle macchine, quali:
- Macchina apriballe: Questa macchina può costituire pericolo quando, per compiere le operazioni di apertura dei colli, l'operatore sale sul nastro trasportatore che può causare cadute accidentali con conseguente trascinamento dall'impannata munita di aculei, con gravi conseguenze per l'incolumità.
- Camera di mista e di fresa: In questa fase della lavorazione il rischio infortunistico può essere dovuto alla mancanza di vie d'uscita nel caso che l'operatore si trovi all'interno box in fase di avanzamento della fresa.
- Battitora: I rischi nell'utilizzo di questa macchina sono dovuti alla presa da parte del tamburo rotante munito di aculei, che può produrre schiacciamento e ferimento degli arti superiori, durante il funzionamento ordinario o per la rotazione dovuta all'inerzia dopo lo spegnimento. Se non è adeguatamente protetta la zona di imbocco si può avere pericolo di presa del lavoratore dalle parti in movimento; lo stesso può avvenire nella ripulitura della vaschetta scarta bottoni.
- Lupa: I rischi connessi con l'utilizzo della lupa sono simili a quelli visti per la battitora.
- Carda Lupo: Anche per questa macchina, i rischi sono simili a quelli di lupa e battitora già viste. Si deve tenere conto dell'esistenza dell'inerzia, dovuta alla massa dei grossi cilindri lavoratori che, anche dopo l’arresto della macchina, continuano a ruotare impiegando alcuni minuti prima di fermarsi.
- Impianto chiuso di oliatura: In caso di apertura dello sportello durante il moto si può avere contatto con l'oleante, con polveri di materiale in lavorazione ed infortuni per contrasto tra le parti in movimento e le parti fisse della macchina.
- Impianto di trasporto pneumatico: I rischi connessi con questo impianto sono dovuti, oltre che al rumore e alle vibrazioni, al pericolo di infortuni per interventi manuali tesi a rimuovere materiale all'ingresso ed all'uscita dei ventilatori centrifughi a seguito di ingolfamenti.
- Esposizione a rumore, dovuto soprattutto agli impianti di aspirazione (90,5 – 96 dBA) e di trasporto pneumatico.
- Esposizione a polveri costituite dalle fibre in lavorazione che si diffondono nell’ambiente di lavoro. La presenza di polveri nel locale è dovuta principalmente al trascinamento di particelle di fibre insieme all'aria immessa nella camera di mista e di fresa dai cicloni di trasporto pneumatico, che fuoriescono dalla parete superiore della camera stessa, necessariamente non a tenuta.
Valori misurati: 4,3 – 4,8 mg/m3.
- Manipolazione di prodotti chimici irritanti, costituiti dagli oleanti che vengono spruzzati sulle fibre. Gli oleanti costituiti in passato da "oleine" vegetali sono ora sostituiti da miscele di oli minerali alto bollenti, da agenti tensioattivi non ionici e da glicoli, ognuno in percentuali variabili intorno al 30%; questi componenti classificano i vari preparati perlomeno nella categoria dei prodotti irritanti per la pelle e per le mucose. Gli oleanti vengono applicati sulle fibre in caduta sotto forma di emulsioni acquose e tale operazione viene eseguita oggi per lo più in oliatori chiusi, che hanno ridotto fortemente l'esposizione degli operatori a queste sostanze.
- Lavoro in prossimità di parti elettriche in tensione, per accesso al quadro elettrico della macchina da parte di personale non specializzato, impianto elettrico non a norma.
- Incendio, rischio dovuto accumulo di polvere delle fibre nei motori elettrici delle macchine e per scintille generate da elettricità statica delle fibre durante il movimento.
3.1.1.4 DANNI NELLA FASE "PREPARAZIONE DELLA MISTA"
3.1.1.4.1 Infortuni anche gravi e talvolta mortali, dovuti a:
- Lesioni per presa e trascinamento dall’impannata munita di aculei della macchina apriballe.
- Lesioni per schiacciamento, presa e trascinamento dalla fresa della camera di mista e di fresa.
- Lesioni per schiacciamento, e ferite agli arti superiori per trascinamento della mano e/o del braccio dalle punte metalliche del tamburo ruotante alla Lupa o alla Battitora.
- Lesioni per trascinamento della mano e/o del braccio alla Carda Lupo
- Ferite per trascinamento, contusioni all’impianto oliatore.
- Ferite e contusioni, per contatto con parti ruotanti all’impianto di trasporto pneumatico.
- Schiacciamento dei piedi in caso di caduta dei cilindri durante la manutenzione alla Carda Lupo.
- Danni uditivi, extrauditivi e disturbo per il rumore generato dall’impianto di aspirazione e dall’impianto di trasporto pneumatico.
- Danni all’apparato respiratorio, per la presenza di polveri. Dalle indagini effettuate non si sono riscontrati danni significativi.
- Irritazione della pelle e degli occhi, per contatto con oleanti e per la presenza di polveri.
- Elettrocuzione, in caso di contatto con parti elettriche in tensione.
3.1.1.5 INTERVENTI ADOTTATI PER ELIMINARE/RIDURRE IL RISCHIO,
FASE "PREPARAZIONE DELLA MISTA"
- Macchina apriballe: Sono state elaborate soluzioni che prevedono l'installazione di un sensore a raggi infrarossi, posizionato a circa quattro metri di altezza sopra il nastro trasportatore, ed un dispositivo che richiede l'intervento manuale dell'operatore per riattivare il moto del nastro trasportatore dopo un tempo di circa due minuti che e quello necessario a percorrere la distanza fino all'impannata (seg. n.116 BD RI-SOL).
- Camera di mista e di fresa: Per ovviare al rischio infortunistico sopra descritto, la camera é provvista di una porta sulla parete contrapposta alla fresa e la fresa stessa è munita di un pulsante di arresto posizionato nella parte interna alla camera. Inoltre, per effettuare la pulizia dell'impannata, fuori dal box viene installato un blocco; per disinserirlo è necessario introdurre nella presa una pulsantiera ad azionamento manuale. Tale pulsantiera ad uomo presente, che costituisce una soluzione ai rischi delle varie fasi di lavorazione del ciclo cardato, una volta inserita nell'apposita presa ad innesto rapido disattiva totalmente tutti i pulsanti ed il quadro di comando della macchina, rimanendo l'unico mezzo di attivazione degli organi in movimento; come illustrato in foto; è essenzialmente costituita da un pulsante senza auto ritenuta, che constringe l'operatore ad una pressione continua per attivare il movimento (segn.RISOL n. 117).
- Per ridurre l’esposizione alle polveri delle fibre in lavorazione, occorre installare un impianto di filtraggio dell’aria immessa nella camera di mista e di fresa dai cicloni di trasporto pneumatico per rimuovere e trattenere le polveri prima dell'immissione nell'ambiente di lavoro o all'esterno.
- Battitora: Le norme di prevenzione prescrivono che i coperchi o sportelli che danno accesso agli organi pericolosi siano saldamente imbullonati e, per eventuali aperture durante la lavorazione, siano dotati del dispositivo di blocco secondo l'art. 72 del D.P.R. 547/55. Nel caso che l'alimentazione della mista avvenga manualmente, la zona di imbocco deve essere protetta lateralmente e superiormente per almeno un metro di lunghezza.
- Lupa: Le protezioni normalmente previste riguardano le zone di imbocco e di uscita, la inamovibilità del coperchio della botte e l'installazione di dispositivi di blocco conformi a quanto prevede l'art. 72 del D.P.R. 547/55. Tale blocco deve essere previsto anche per il portello di accesso alla moscaiola, se da questa zona vi è la possibilità di entrare in contatto con gli organi lavoratori della botte.
- Carda Lupo: Le norme di prevenzione prevedono che le parti più pericolose, come gli organi alimentatori o ingollini, i cilindri lavoratori e spogliatori, il volano di uscita e gli organi di trasmissione del moto siano racchiusi in appositi carter muniti di blocco che impediscano l'accesso quando gli organi sono in movimento. Le operazioni di pulizia e manutenzione devono essere effettuate a macchina ferma. Le soluzioni realizzate sono le seguenti:
- dispositivo di blocco costituito da un interruttore su cui agisce una vite con lunga filettatura, dotata di pomello, che aziona inizialmente l'arresto della macchina ma non consente lo sblocco dei carter degli organi di trasmissione del moto finché non è completata la svitatura del dispositivo, cioè a macchina ferma (segn.119 RISOL);
- barra solidale al coperchio del gran tamburo che rimane bloccato finché non è avvenuta l'apertura dei carter precedenti, cioè a macchina completamente ferma;
- microinterruttore che sente la posizione di apertura o chiusura di quest'ultimo coperchio.
Per rendere possibile la rimessa in moto della macchina, tutti i dispositivi sopra elencati devono essere reinseriti in sequenza inversa
- Impianto chiuso di oliatura: Lo sportello apribile è dotato di microinterruttore per evitare l'apertura dello stesso con la macchina in movimento. Questo dispositivo di blocco può essere disinserito solo con l'uso di un pulsante ad uomo presente come già descritto. I punti di presa devono essere adeguatamente protetti tramite opportuni carter sagomati. La soluzione è rivolta sia al rischio infortunistico, sia alla possibilità di contatto con l’oleante.
- Impianto di trasporto pneumatico: Le soluzioni per il rischio infortunistico consistono nell'installazione dei dispositivi di blocco sui portelli di ispezione, generalmente costituiti da un interruttore con vite a lunga filettatura (segn.119 RISOL).
- Per ridurre l’esposizione a rumore, occorre una adeguata progettazione degli impianti ed isolamento acustico.
- Per ridurre la possibilità di contatto con gli oleanti è necessario utilizzare impianti chiusi di oliatura come sopra descritti.
3.1.1.6 INDICAZIONE DI EVENTUALE APPALTO A DITTA ESTERNA PER LA FASE "PREPARAZIONE DELLA MISTA"
In genere questa fase non viene appaltata.
- RIFERIMENTI LEGISLATIVI E NORME TECNICHE PER LA FASE "PREPARAZIONE DELLA MISTA"
- D.P.R. 547/55
- D.Lgs. 277/’91
- D.P.R. 303 / ’56
- Norma UNI EN ISO 11111 del Luglio 1997
3.1.1.8 IMPATTO ESTERNO della fase "PREPARAZIONE DELLA MISTA"
Emissioni in atmosfera di polveri delle fibre tessili in lavorazione: non si ha produzioni di emissioni verso l’esterno in questa fase.
Diffusione di rumore nell’ambiente circostante: Generalmente la preparazione della mista viene effettuata durante il turno di lavoro diurno pertanto la diffusione di rumore proveniente da questa fase generalmente non crea grossi fastidi alla popolazione circostante in quanto sono presenti altre sorgenti rumorose di fondo in particolare traffico veicolare.
Produzione di rifiuti: non si ha produzione di rifiuti di processo.
Utilizzo di oleanti e tensioattivi: L’utilizzo di queste sostanze non costituisce un impatto diretto sull’ambiente durante il ciclo di lavorazione della filatura, ma il problema si verifica nei cicli di lavorazione successiva (tintorie, rifinizioni, ecc…) che prevedono le fasi di lavaggio e di asciugatura con conseguenti scarichi idrici ed immissioni in atmosfera. E’ pertanto necessario utilizzare oleanti e tensioattivi del tipo meno nocivo per l’ambiente.
3.1.2 ANALISI DEI RISCHI, DANNI E SOLUZIONI nella fase "CARDATURA"
1. FASE DI LAVORAZIONE : CARDATURA
2. COD.INAIL :
3. FATTORE DI RISCHIO : Rischi per la salute e igienico ambientali:
esposizione a polveri (fibre tessili);
esposizione a rumore.
Rischi per la sicurezza:
carenza di sicurezza su macchine (lavoro in prossimità di organi meccanici in movimento);
carenza di sicurezza elettrica.
4. CODICE DI RISCHIO :
5. N.ADDETTI :
3.1.2.1 DESCRIZIONE DELLA FASE "CARDATURA"
Dal reparto preparazione il materiale viene inviato ai box di stoccaggio dove rimane depositato in attesa di essere richiamato per essere avviato alla operazione di cardatura, la quale costituisce l'operazione centrale dell'intero processo.
Il macchinario che la realizza è detto "assortimento di carderia" ed effettua le seguenti operazioni:
- mescola intimamente le fibre per arrivare alla massima omogeneità.
- elimina ulteriormente le fibre corte e le impurità dall'ammasso fibroso.
- parallelizza ed ordina le fibre per ottenere un velo dimensionalmente regolare, perfettamente omogeneo e con peso costante per unità di superficie.
- suddivide il velo in stoppini tramite un divisore.
- prepara gli stoppini per la filatura.
L'operazione di cardatura avviene per mezzo del passaggio delle materie prime attraverso vari cilindri molto vicini fra loro, forniti sulla superficie di guarnizioni dotate di punte metalliche, che provocano l'apertura del materiale e il reciproco scorrimento delle fibre con conseguente parallelizzazione delle stesse.
3.1.2.2 ATTREZZATURE E MACCHINE UTILIZZATE NELLA FASE "CARDATURA"
L’assortimento di carderia è una macchina di grandi dimensioni, che può raggiungere 40 metri di lunghezza, 2 - 3 metri di larghezza, ed altezza superiore a 2 metri sopra il livello del pavimento e generalmente con una parte anche sotto il livello del piano di calpestio cui si accede tramite l’apposita fossa sottocarda.
Per ogni assortimento di carderia si possono individuare le seguenti zone di lavoro:
- zona di alimentazione
- zona di cardatura
- zona di uscita
- fossa sottocarda
Zona di alimentazione dell’assortimento di carderia
Inizia con il caricatore che ha lo scopo di alimentare in modo regolare le carde. Il flusso di materiale dal reparto preparazione arriva nella parte superiore di un cassone sopraelevato. Da questo il materiale viene prelevato da due rulli scanalati che ruotando lo fanno cadere in una camera di riserva sottostante il cui livello viene mantenuto costante tramite rilevatori volumetrici collegati con la rotazione dei cilindri suddetti. Un trasportatore orizzontale porge poi le fibre ad un'impannata costituita da un trasportatore inclinato munito di punte metalliche che va ad alimentare una bilancia la quale a sua volta fornisce le fibre in quantità regolata e costante alla prima carda o avantreno dell'assortimento. Per le operazioni di pulizia e manutenzione si accede al cassone sopraelevato tramite uno sportello posto sopra i rulli scanalati e alla sottostante camera di deposito tramite uno sportello incernierato in basso.
Le fibre provenienti dal caricatore passano sotto un cilindro premitore poi vengono prese da due o coppie di due cilindri alimentatori o ingollini; da questi passano ad un cilindro di alimentazione anch’esso dotato di punte metalliche detto rubàno, che ruota con velocità periferica maggiore rispetto agli ingollini e porge le fibre al gran tamburo.
Zona di cardatura dell’assortimento di carderia
La zona di cardatura è formata da varie parti le quali possono essere presenti tutte o meno: l’avantreno, le carde a rompere, il trasportatore, le carde traverse, il pettinatore, gli organi di trasmissione del moto, la botte o M, la carda a dividere, la fossa sottocarda. L'avantreno è unico mentre le carde a rompere e le carde traverse possono essere una o più di una. Il numero delle carde nell'assortimento può variare in rapporto al titolo del filato che si deve ottenere.
Ogni carda è essenzialmente costituita dal gran tamburo, cilindro di grandi dimensioni che ruota a velocità periferica molto elevata, sul quale si trovano le coppie dei cilindri lavoratore e spogliatore, detti gruppi cardanti, in numero variabile, da cinque a sette, in rapporto al titolo da raggiungere per il filato. Il cilindro lavoratore preleva le fibre non allineate dal gran tamburo. Queste vengono poi recuperate dal cilindro spogliatore e reimmesse sul gran tamburo e da questo ancora lavorate nel gruppo cardante successivo.
Il gran tamburo e i gruppi cardanti dell'avantreno sono dotati di guarnizioni con punte metalliche rigide mentre nelle altre carde le guarnizioni sono dotati di punte metalliche flessibili.
La zona di uscita di ogni carda è generalmente formata dal volano e dal sottovolano. Il volano è un cilindro dotato di guarnizioni a punte metalliche lunghe e flessibili. Il sottovolano è un cilindro di dimensioni più piccole che rimuove l'eccedenza di fibre che possono rimanere sul volano e le reimmette sul gran tamburo. Dopo l'ultimo gruppo cardante le fibre vengono inviate al pettinatore.
Il pettinatore è un cilindro di grandi dimensioni che, ruotando con velocità periferica inferiore a quella del gran tamburo, effettua una condensazione delle fibre trasportate.
Un pettine oscillante poi provvede a distaccare il velo delle fibre per passarlo alle operazioni successive; in uscita dalla carda a rompere il velo di fibre viene ripreso dal trasportatore.
Sotto la prima coppia cardante delle carde traverse e delle carde a dividere si trova installata la vaschetta mangiapelo che svolge la funzione di raccogliere ed allontanare l'eccesso di fibre corte.
Trasportatore affaldatore: Tra le carde a rompere e le carde traverse si trova il trasportatore. Questa parte della macchina effettua una rotazione di 90° ed un affaldamento del velo delle fibre in uscita dall'ultima carda a rompere, che viene poi inviato agli ingollini della prima carda traversa. E' costituito dall'affaldatore e dai trasportatori orizzontali e verticali. Il percorso di questi ultimi può essere dislocato sopra o sotto il livello del pavimento.
Epuratore o schiacciapunte: Si trova all'uscita dell'ultima carda traversa, dopo il pettinatore. E' costituito da due cilindri di acciaio levigati a specchio, fortemente pressati uno sull'altro, attraverso i quali passa il velo in lavorazione. Ha il compito di polverizzare i frammenti vegetali che possono ancora trovarsi nel velo.
Botte o M: Costituisce un polmone di stoccaggio del velo di fibre in lavorazione tra le carde e i divisori che possono essere uno o più di uno.
Organi di trasmissione del moto: Le vecchie macchine di carderia sono generalmente dotate di un unico motore che aziona tutti gli organi principali e quelli accessori.
Si tratta quindi di un sistema esteso e complesso di organi di trasmissione del moto costituito da pulegge, cinghie di trasmissione, ingranaggi, che si sviluppa lungo tutta la fiancata della macchina dal quale si può accedere in molti casi, per la rimozione delle protezione, agli organi lavoratori delle carde, se questi non sono adeguatamente protetti.
Alcuni assortimenti più moderni dispongono di carter per ogni organo di trasmissione o per gruppi di essi, incernierati e fermati da chiusure a scatto con magneti e pomelli per l'apertura.
Fossa sottocarda: E' costituita da un vano situato al di sotto del pavimento, a cui si accede tramite scale, in corrispondenza della parte inferiore dei diversi gruppi di carde e del divisore. E' chiusa da una botola posta a livello del pavimento e/o da un cancello posto all'ingresso del vano.
Vi vengono svolte periodicamente operazioni di rimozione delle fibre scartate dalle macchine, pulizia e controlli vari.
Impianto di pulitura automatica: E’ installato nelle macchine di più recente costruzione in corrispondenza del gran tamburo, sia nella parte esterna che nella fossa sottocarda.
Zona di uscita dell’assortimento di carderia:
La zona di uscita è essenzialmente costituita dal divisore che ha lo scopo di sezionare il velo in piccole strisce della larghezza di circa 1 cm che vengono poi arrotondate per stropicciamento ed avvolte in ciambelle. Il divisore viene alimentato direttamente dall’ultima carda nel caso di "assortimento a treno" oppure dalla botte o M. Il divisore è formato dalla carda a dividere e dal castello. Il divisore si trova in parte al disotto del pavimento e vi si accede dalla fossa sottocarda.
La carda a dividere è costituita è costituita da cilindri scanalati che hanno la funzione di dividere il velo formando le piccole strisce. Il castello del divisore è rivolto verso l'uscita ed ha la funzione di stropicciare le piccole strisce trasformandole in stoppini, che vengono poi avvolti su dei subbi di legno, tramite manicotti flottatori o "trombe".
Per sorvegliare la qualità degli stoppini è necessaria una buona illuminazione dell'interno del divisore.
3.1.2.3 FATTORI DI RISCHIO NELLA FASE "CARDATURA"
- Lavoro in prossimità di organi meccanici in movimento, costituiti da:
- Caricatore: Il portello del cassone superiore consente l’accesso ai cilindri ruotanti, e il portello inferiore consente l’accesso all'impannata munita di punte. Pertanto, esiste il rischio di presa e trascinamento qualora l’operatore intervenga manualmente per rimuovere eventuali ingolfamenti o manutenzione.
- Zona di alimentazione delle carde: I rischi più noti di questa parte del macchinario riguardano gli ingollini ed il rubáno che presentano zone di presa e che possono necessitare di interventi da parte degli operatori durante la lavorazione.
- Zone di cardatura e di uscita delle carde: In questa fase le operazioni più a rischio risultano essere:
- asportazione manuale di ciuffi di peluria che si possono formare ai bordi dei cilindri lavoratori, nelle vaschette mangiapelo e sugli organi di trasmissione del moto;
- rimozione di materiale in lavorazione in caso di ingolfamento per sovraccarico;
- soffiatura con aria compressa per pulizia della macchina nel cambio di materiale in lavorazione.
- Trasportatore, affaldatore: Possono essere presenti rischi di cesoiamento o di presa fra ingranaggi da parte delle impannate superiori, dai trasportatori oscillanti del velo e da altre parti in movimento.
- Epuratore o schiacciapunte: poiché possono essere necessari interventi per l'introduzione del velo all'inizio della lavorazione di una nuova mista i lavoratori possono essere sottoposti al rischio di presa tra i due cilindri contrapposti.
- Divisore: In questa macchina sono talvolta necessari interventi sulle cosiddette trombe o sulle cinghie di gomma per riprendere gli stoppini che si sono staccati o per l'eliminazione delle rolle con il rischio di presa della mano.
- Organi di trasmissione del moto alle carde: i rischi sono quelli generali degli organi di trasmissione, accentuati dalla loro estensione e dalla notevole inerzia delle carde per che può durare anche un minuto.
- Fossa sottocarda: Dalla fossa sottocarda possono essere accessibili, se non adeguatamente protette, le parti inferiori dei vari organi lavoratori di cui è costituito l'assortimento e i vari meccanismi di trasmissione del moto; ciò comporta rischi analoghi a quelli già visti in precedenza per la parte posta sopra il piano di calpestio.
La pulizia automatica della parte inferiore del gran tamburo, viene eseguita a macchine in movimento tramite aspiratori automatici che scorrono trasversalmente (cavallino).
- Esposizione a rumore: 86 – 87 dBA con picchi fino a 104 dBA all’avviamento della macchina.
- Contatti diretti con parti elettriche in tensione, costituite dalle lampade per illuminazione della zona di uscita e del porta subbi. Il pericolo è aggravato dal fatto che le lampade sono installate in prossimità di grandi masse metalliche.
- Esposizione a polveri di fibre tessili, costituite dalle fibre in lavorazione, durante le operazioni di rimozione della peluria accumulata nella fossa sottocarda.
3.1.2.4 DANNI NELLA FASE "CARDATURA"
- Infortuni anche gravi e talvolta mortali, dovuti a:
- Ferite e contusioni per presa e trascinamento al caricatore.
- Ferite e contusioni per presa e trascinamento alle carde (organi di alimentazione, lavoratori, trasmettitori del moto e fossa sotto-carda).
- Ferite, contusioni e amputazioni per presa e trascinamento al trasportatore affaldatore.
- Ferite e contusioni per presa e trascinamento all’epuratore (o schiacciapunte).
- Ferite e contusioni per presa e trascinamento al divisore.
- Morte per folgorazione elettrica al divisore.
- Danni uditivi, extrauditivi e disturbo in relazione ai valori di esposizione al rumore.
- Danni all’apparato respiratorio, per l’esposizione a polveri di fibre tessili nella fossa sottocarda.
3.1.2.5 INTERVENTI ADOTTATI PER ELIMINARE/RIDURRE IL RISCHIO NELLA FASE "CARDATURA"
Considerando che in molte delle operazioni di seguito descritte verrà introdotto l'uso della pulsantiera ad uomo presente, si rendono necessarie alcune precisazioni rispetto a quanto già illustrato precedentemente. L'indirizzo delle norme antinfortunistiche prevede di ridurre al limite minimo i pericoli che derivano dalla rimozione delle protezioni, pertanto l'inserimento della pulsantiera deve consentire la disattivazione dei carter e delle reti soltanto nella zona interessata. Alla luce di quanto sopra descritto nell'assortimento di carderia si devono identificare le zone seguenti quella della fossa sottocarda e quella al di sopra del piano di calpestio che a sua volta verrà divisa nel numero delle carde componenti l'assortimento. Per rendere più agevole l'azione degli addetti, la pulsantiera può essere radiocomandata purché sul quadro di comando sia installato un commutatore che abiliti il radiocomando stesso, escludendo gli altri comandi di movimento delle carde.
- Caricatore: Il portello del cassone superiore viene dotato di dispositivo di blocco ex art. 72 per evitare il pericolo di presa fra i cilindri o fra uno dei cilindri e la parete adiacente. Per evitare pericoli di presa tra il cilindro superiore e la parete adiacente o dall'impannata munita di punte lo sportello inferiore può essere dotato di due sistemi alternativi:
- dispositivo di blocco che impedisce l'apertura a macchina in moto (art. 72 c.s.) e pulsantiera per movimento a scatti ad uomo presente in caso di rimozione del blocco;
- barra distanziatrice trasversale che impedisce l'accesso alla camera anche con sportello aperto e carter di protezione tra il cilindro scanalato sovrastante e adiacente alla parete e la parete stessa per consentire le operazioni di pulitura con aria compressa.
- Zona di alimentazione delle carde (ingollini, rubáno): Questi organi devono essere dotati di coperchi chiusi e di dispositivi di blocco ex art. 72. La zona di imbocco deve essere costruita in modo da impedire il contatto accidentale dei lavoratori con gli organi in movimento. Nel caso di macchine non corrispondenti alle norme di sicurezza sono state installate bandelle metalliche o in plexiglas larghe venti, venticinque centimetri e solidali con il coperchio di protezione degli organi alimentatori.
- Zone di cardatura e di uscita delle carde: le norme di prevenzione prevedono che le custodie, di cui devono essere dotati gli organi lavoratori, devono essere conformate in modo da rendere impossibile il contatto con le mani o altre parti del corpo degli operatori e che siano rese inamovibili. Se durante il lavoro devono essere aperte o spostate queste devono essere provviste del dispositivo di blocco. Pertanto tutti gli organi lavoratori (gran tamburo, cilindri lavoratori e spogliatori, volani, rubano ecc.), escluso il pettinatore, devono essere racchiusi da custodie rese inamovibili da bulloni o viti. Le parti della macchina che devono essere aperte durante la lavorazione, la manutenzione o la pulitura, quali carter, cuffie, sportelli, ecc. devono essere apribili con sistemi dotati di dispositivo di blocco come previsto dall'Art. 72 DPR 547 /55.
Le zone di presa laterali, ad esempio tra pettinatore e sottovolano se non sono adeguatamente protette dai coperchi, devono essere dotate di apposite bandelle.
Qualora sia possibile l'introduzione delle mani all'interno della vaschetta mangiapelo devono essere predisposti adeguati prolungamenti per impedirlo.
- Trasportatore, affaldatore: tutte le parti che si trovano ad una altezza inferiore a metri 2.5 dal piano di calpestio, devono essere adeguatamente segregate. Nei casi in cui il trasporto del velo attraversi il piano di calpestio, deve essere predisposta una fascia ferma piede, alta almeno venti centimetri, a protezione dell'apertura sul pavimento.
- Epuratore o schiacciapunte: vengono date indicazioni perché il velo non venga porto manualmente ma con l'ausilio di un'apposita stecca. Deve essere installata inoltre una barriera rigida inamovibile in corrispondenza delle fiancate laterali, posizionata e conformata in modo da impedire di raggiungere con la mano i punti di presa tra i cilindri e consentire il passaggio della stecca per sostenere il velo delle fibre in lavorazione.
- Divisore: Gli interventi sulle trombe o sulle cinghie di gomma devono essere eseguiti o usando appositi ganci che mantengano la mano distante dagli organi di presa oppure a macchina ferma o facendo uso della pulsantiera ad uomo presente. Per gli interventi che devono essere eseguiti accedendo alla fossa sottocarda valgono le indicazioni sotto riportate.
- I dispositivi illuminanti ed ausiliari posti all'interno del divisore devono essere protetti da plafoniere resistenti agli urti e, poiché questi sono installati in prossimità di grandi masse metalliche, le linee devono essere alimentate a 24 volt con avvolgimenti primario e secondario dei trasformatori separati tra loro o con l'installazione sulle linee di un interruttore ad alta sensibilità (ID
n = 10 mA). I cinematismi posti lateralmente al castello del divisore devono essere segregati e protetti per evitare il rischio di cesoiamento.
- Organi di trasmissione del moto alle carde: per rimuovere queste condizioni di rischio la norma prevede, la segregazione di questi organi di trasmissione per un'altezza dal pavimento non inferiore a due metri, realizzabile tramite robuste paratie o reti conformate in modo da rendere impossibile il contatto. Qualora tali custodie proteggano anche gli organi lavoratori, queste devono essere dotate di dispositivi di blocco conformi all'art.72. Non sono ammessi i dispositivi di protezione semplicemente chiudibili a scatto. Una soluzione semplice ed efficace consiste nel bloccare con i coperchi degli organi lavoratori le paratie laterali degli organi di trasmissione che dovranno comunque essere provvisti di fine corsa elettrico (segn.120 RISOL).
- Fossa sottocarda: la botola o il cancello di accesso alla fossa devono essere dotati di dispositivo di blocco. Qualora sussista la necessità di intervenire con le carde in movimento per controlli audiovisivi, manutenzioni ecc... tali controlli possono essere eseguiti soltanto facendo uso della pulsantiera ad uomo presente, già descritta. La rimozione della polvere e della peluria accumulata deve essere eseguita a macchina ferma con l'uso di appositi aspirapolvere.
Per la pulizia automatica della parte inferiore del gran tamburo, devono essere predisposti appositi prolungamenti fissi della zona di imbocco del tubo aspirante per evitare qualsiasi contatto con le guarnizioni della carda.
Tutta la fossa sottocarda deve essere adeguatamente illuminata e l'impianto elettrico deve presentare un grado di protezione non inferiore a IP 44.
- Per ridurre l’esposizione a polveri di fibre tessili nella fossa sottocarda è necessario installare e tenere efficienti sistemi di aspirazione meccanica.
3.1.2.6 INDICAZIONE DI EVENTUALE APPALTO A DITTA ESTERNA PER LA FASE "CARDATURA"
Questa fase non viene mai appaltata in quanto costituisce la fase centrale di tutto il processo.
3.1.2.7 RIFERIMENTI LEGISLATIVI E NORME TECNICHE PER LA FASE "CARDATURA"
- D.P.R. 547/55
- D.Lgs. 277/’91
- D.P.R. 303 / ‘56
- Norma UNI EN ISO 11111 del Luglio 1997
3.1.2.8 IMPATTO ESTERNO della fase "CARDATURA"
Emissioni in atmosfera di polveri delle fibre tessili in lavorazione: non si hanno emissioni significative. Possono essere presenti eventuali impianti di condizionamento aria ambiente.
Diffusione di rumore nell’ambiente circostante: Generalmente le macchine dell’assortimento di carderia sono le più rumorose del ciclo. D’altra parte, essendo la fase centrale dell’intero processo, anche la disposizione delle macchine è in genere al centro dello stabilimento produttivo (a differenza del reparto filatura che essendo l’ultima fase si trova vicino alle pareti esterne dello stabilimento). Pertanto il rumore prodotto da questa fase, contribuisce alla rumorosità generale prodotta dall’esercizio della attività ma non è identificabile all’esterno come rumore prevalente.
Un’altra fonte di rumore per l’esterno è costituita dagli impianti di aspirazione delle pelurie, derivante sia dai motori elettrici necessari a creare la depressione per l’aspirazione, sia dalla parte terminale delle condotte di aspirazione le quali finiscono in contenitori (in genere sacchi o box) di raccolta delle pelurie dove l’aria uscendo a pressione genera rumore.
Nella nostra zona, un caso significativo degli ultimi anni, ha riguardato una filatura nel Comune di Montemurlo contro la quale si è avuto solo un esposto all’Autorità competente per il rumore da essa diffuso nell’ambiente circostante di giorno proveniente dai reparti preparazione, cardatura e filatura e di notte dal reparto filatura.
Nella relativa indagine svolta dall’ARPAT di Prato negli anni 93-95 si è verificato il superamento del limite di accettabilità pari a 70 dBA durante il periodo diurno arrivando a 75 dBA misurato sul marciapiede ad un metro dalla parete perimetrale dei locali produttivi. Va fatto comunque presente che durante il periodo di osservazione era presente un consistente un rumore di fondo dovuto al traffico veicolare che misurato con ditta ferma è risultato pari a 72 dBA. Invece di notte la misurazione del rumore ambientale è risultato pari a 57.5 dBA, quindi inferiore ai 60 dBA previsti come limite di accettabilità per quella zona durante il periodo notturno.
Le misure effettuate nella abitazione del reclamante ubicata di fronte alla filatura dall’altra parte della strada ha dato un valore differenziale di 0.1 dBA durante il giorno rientrando quindi nel valore limite differenziale per il giorno di 5 dBA, mentre di notte a seconda dell’ora il valore differenziale variava tra 0.1 a 3.3 dBA, superando quindi il valore limite differenziale per la notte di 3 dBA.
In definitiva la vicenda si è conclusa con l’emissione di una ordinanza da parte del Comune di Montemurlo con la quale si imponeva alla ditta di mantenere finestre e portoni chiusi durante la lavorazione diurna e notturna oltre ad installare un adeguato impianto di ricambio dell’aria per il benessere degli addetti. Inoltre la ditta ha provveduto ad insonorizzare con pannelli di materiale fonoassorbente il portone di accesso ed il locale dove sono ubicati i motori elettrici per la pulitura del reparto carderia.
Produzione di rifiuti: La peluria residua del processo è stata fino ad oggi recuperata di norma o all’interno del processo stesso, o come materiale quotato in Borsa o come materiale destinato al riutilizzo. Prima del Decreto "Ronchi" tali materiali non erano soggetti a registrazione o a denuncia (M.U.D.) e pertanto non è possibile quantificarne la produzione. I quantitativi minimi di rifiuti non riutilizzati di questo processo sono stati nella maggior parte dei casi equiparati ai rifiuti urbani e smaltiti tramite l’azienda mucipalizzata.
3.1.3 ANALISI DEI RISCHI, DANNI E SOLUZIONI nella fase "MANUTENZIONE, PULITURA E CONTROLLO SULLE MACCHINE DI CARDERIA
"
1. FASE DI LAVORAZIONE : MANUTENZIONE PULITURA E CONTROLLO DELLE MACCHINE DI CARDERIA
2. COD.INAIL :
3. FATTORE DI RISCHIO : Rischi per la salute e igienico ambientali:
esposizione a polveri (fibre tessili).
Rischi per la sicurezza:
carenza di sicurezza su macchine (lavoro in prossimità di organi meccanici in movimento);
Rischi trasversali o organizzativi:
movimentazione manuale dei carichi.
4. CODICE DI RISCHIO :
5. N.ADDETTI :
- DESCRIZIONE DELLA FASE "MANUTENZIONE, PULITURA E CONTROLLO SULLE MACCHINE DI CARDERIA"
Nel ciclo di lavorazione della cardatura sono spesso necessarie una serie di operazioni complementari che presentando forti rischi, richiedono particolare attenzione e devono essere eseguite direttamente da personale esperto o sotto la sua sorveglianza. Vediamo più in dettaglio in cosa consistono tali operazioni:
- Reinserimento degli organi di sgrano degli ingollini dell'avantreno, con macchina in movimento: Nelle carde disposte di "sgrano" meccanico, il quale entra in funzione in presenza di accumuli di materiale, distaccando uno degli ingollini rispetto a quello cui è contrapposto.
- Sfasciatura del rubáno: Questa operazione si rende necessaria quando non vengono sufficientemente rimosse le fibre dal sottovolano ed accade che queste formano delle fasciature che ricoprono le punte metalliche.
- Pulitura a striscio per la manutenzione delle guarnizioni del gran tamburo: Si tratta di operazioni di molatura, arrotatura, rettifica e simili che vengono eseguite con appositi attrezzi denominati pianino, cardino o ferro, i quali vengono portati a contatto con le guarnizioni in modo manuale o automatico, mentre il gran tamburo ruota in senso inverso a quello di normale funzionamento della carda.
- Arrotatura e rettifica delle guarnizioni dei cilindri lavoratori su banco: i cilindri lavoratori vengono trasportati, manualmente o con l’ausilio di carrelli o paranchi, su banchi di arrotatura automatica. La rotazione dei cilindri viene attuata tramite motori elettrici fissi o portatili.
- Interventi su organi di trasmissione del moto ai cilindri lavoratori e spogliatori che si rendono necessari in caso di sovraccarico della carda.
- Pulizia della macchina con aria compressa: avviene effettuata alla fine della giornata di lavoro o al cambio di partita specialmente in caso di fibre di colore diverso.
3.1.3.2 ATTREZZATURE E MACCHINE UTILIZZATE PER LA FASE "MANUTENZIONE, PULITURA E CONTROLLO SULLE MACCHINE DI CARDERIA"
3.1.3.2 PIANINO, CARDINO, FERRO.
Sono attrezzi utilizzati per la molatura, arrotatura, rettifica delle guarnizioni metalliche del gran tamburo mentre questo ruota.
3.1.3.3 FATTORI RISCHIO NELLA FASE "MANUTENZIONE, PULITURA E CONTROLLO SULLE MACCHINE DI CARDERIA"
3.1.3.3.1 Lavoro in prossimità di organi meccanici in movimento, costituiti da:
- Organi di sgrano, ingollini durante il loro reinserimento con macchina in movimento.
- Rubáno: durante la sfasciatura delle fibre tessili accumulate intorno ad esso, esiste il rischio di contatto con le punte metalliche e il rischio di presa e trascinamento degli arti superiori.
- Guarnizioni del gran tamburo: durante la pulitura a striscio manuale, esiste il rischio di presa e trascinamento.
- Guarnizioni dei cilindri lavoratori: durante l’arrotatura e rettifica a banco, esiste il rischio di ferite agli arti superiori per contatto con le punte metalliche in rotazione.
- Organi di trasmissione del moto ai cilindri lavoratori e spogliatori durante gli interventi di rimozione delle fibre in caso di sovraccarico della carda oppure durante l’oliatura e la pulitura mediante aria compressa durante il moto. In tali operazioni gli addetti possono essere fortemente esposti al pericolo di presa da parte di questi organi pericolosi.
- Movimentazione manuale dei carichi, per il trasporto delle guarnizioni dei cilindri dalle macchine al banco di lavoro per la manutenzione. Il rischio infortunistico è aggravato dal fatto che le guarnizioni sono dotate di punte metalliche.
- Esposizione a polveri di fibre tessili, le quali si diffondono nell’ambiente di lavoro durante la pulitura con aria compressa.
3.1.3.4 DANNI NELLA FASE "MANUTENZIONE, PULITURA E CONTROLLO SULLE MACCHINE DI CARDERIA"
3.1.3.4.1 Infortuni:
- Ferite e contusioni in caso di presa e trascinamento dagli organi meccanici in movimento o di contatto con le punte metalliche delle guarnizioni.
- Danni all’apparato muscolo-scheletrico, si possono verificare durante la movimentazione manuale delle guarnizioni.
3.1.3.4.1.2 Schiacciamento e ferite dei piedi, in caso di caduta delle guarnizioni durante la movimentazione manuale.
3.1.3.4.2 Danni all’apparato respiratorio: per la presenza di polveri durante la pulizia con aria compressa.
3.1.3.5 INTERVENTI PREVENZIONISTICI PER LA FASE "MANUTENZIONE, PULITURA E CONTROLLO SULLE MACCHINE DI CARDERIA"
- Il reinserimento degli organi di sgrano degli ingollini dell'avantreno, con macchina in movimento può essere consentito senza fermare la carda solamente facendo uso delle apposite leve o dispositivi preposti allo scopo. La rimozione del materiale accumulato deve avvenire a macchina ferma.
- Sfasciatura del rubáno: La rimozione delle fibre dal sottovolano deve essere eseguita a macchina ferma, usando appositi attrezzi per evitare ferite dovute alle punte metalliche delle guarnizioni. Eventuali rotazioni del rubàno per completare la sfasciatura devono essere eseguite manualmente oppure tramite la pulsantiera ad uomo presente.
- Pulitura a striscio per la manutenzione delle guarnizioni del gran tamburo: Nei casi in cui tali operazioni non vengano eseguite automaticamente devono essere seguite le seguenti indicazioni:
- gli interventi devono essere effettuati soltanto da personale esperto.
- quando l'operazione viene effettuata nella parte superiore del gran tamburo deve essere predisposto un piano di appoggio per il lavoratore stabilmente fissato alla macchina, confortevole e dotato di un robusto parapetto sul lato verso il gran tamburo.
- se l'intervento è effettuato dal pavimento nella parte posteriore della macchina, devono essere forniti al lavoratore maschere o occhiali di protezione dalla polvere e particelle di sporcizia.
- gli utensili che si impiegano in queste operazioni ,quali pianino, cardino spazzola ecc., devono essere facilmente impugnabili e costruiti in modo da proteggere le mani.
- Arrotatura e rettifica delle guarnizioni ed operazioni simili effettuate su banco: Gli organi di trasmissione o le parti pericolose in movimento delle macchine su cui viene effettuata l'arrotatura devono essere protette adeguatamente. La rimozione ed il rimontaggio dei cilindri deve avvenire con l'ausilio di sollevatori meccanici ed i lavoratori devono essere dotati di indumenti di protezione contro lo schiacciamento dei piedi e ferite dovute alle punte metalliche.
- Interventi su organi di trasmissione del moto ai cilindri lavoratori e spogliatori: Dopo aver rimosso i cilindri dalla propria sede a macchina ferma si può procedere allo spurgo del materiale in eccesso facendo ruotare la carda con l'uso della pulsantiera ad uomo presente. in questa fase in tal modo si può procedere anche ad effettuare i controlli audiovisivi ad operazione avvenuta.
- Oliatura o pulizia della macchina con aria compressa: Queste operazioni possono essere eseguite a macchina in moto soltanto quando tra l'operatore e la macchina è frapposta una barriera resistente in rete metallica o simile alta almeno due metri, con fori tali da consentire il passaggio dei beccucci per oliare o le canne per il soffiaggio con l'aria ma che non consenta in alcun modo il passaggio della mano su tutti i lati di accesso possibili. I beccucci degli oliatori devono essere lunghi almeno 50 cm. Le canne per l'aria compressa devono essere dotate di cannello di prolunga all'estremità costituito da materiale frangibile in modo che possa facilmente frantumarsi in caso di presa dagli organi in movimento. Durante la soffiatura con aria compressagli addetti devono utilizzare mascherine di protezione da polveri.
3.1.3.6 APPALTI A DITTE ESTERNE PER LA FASE "MANUTENZIONE, PULITURA E CONTROLLO SULLE MACCHINE DI CARDERIA"
Questa fase generalmente non viene appaltata.
3.1.3.7 RIFERIMENTI NORMATIVI PER LA FASE "MANUTENZIONE, PULITURA E CONTROLLO SULLE MACCHINE DI CARDERIA"
- D.P.R. 547/55
- D.Lgs. 277/’91
- D.P.R. 303 / ’56
- Norma UNI EN ISO 11111 del Luglio 1997
3.1.3.8 IMPATTO ESTERNO della fase "MANUTENZIONE, PULITURA E CONTROLLO SULLE MACCHINE DI CARDERIA"
Emissioni in atmosfera di polveri delle fibre tessili in lavorazione: non esistono emissioni significative.
Diffusione di rumore nell’ambiente circostante: In questa fase il rumore proviene principalmente dalla soffiatura con aria compressa delle macchine alla fine di ogni turno di lavoro. Il rumore è determinato sia dal sibilo delle pistole ad aria compressa sia dall’entrata in funzione del compressore dell’aria. In genere il compressore è di grandi dimensioni e fornisce l’aria compressa a tutto lo stabilimento tramite un sistema canalizzato, quindi l’impatto è circoscritto a dove è ubicato il compressore che il genere viene posto in un box o in un locale sul retro della ditta. Al momento non sono pervenuti esposti da parte della popolazione per il rumore proveniente dai compressori.
Produzione di rifiuti: La peluria residua del processo è stata fino ad oggi recuperata di norma o all’interno del processo stesso, o come materiale quotato in Borsa o come materiale destinato al riutilizzo. Prima del Decreto "Ronchi" tali materiali non erano soggetti a registrazione o a denuncia (M.U.D.) e pertanto non è possibile quantificarne la produzione. I quantitativi minimi di rifiuti non riutilizzati di questo processo sono stati nella maggior parte dei casi equiparati ai rifiuti urbani e smaltiti tramite l’azienda mucipalizzata.
3.1.4 ANALISI DEI RISCHI, DANNI E SOLUZIONI nella fase "FILATURA"
1. FASE DI LAVORAZIONE : FILATURA
2. COD.INAIL :
3. FATTORE DI RISCHIO : Rischi per la salute e igienico ambientali:
esposizione a rumore;
esposizione a microclima sfavorevole;
esposizione a polveri (fibre tessili).
Rischi per la sicurezza:
carenza di sicurezza su macchine (lavoro in prossimità di organi meccanici in movimento);
utilizzo di attrezzature manuali taglienti.
Rischi trasversali o organizzativi:
movimentazione manuale dei carichi.
4. CODICE DI RISCHIO :
5. N.ADDETTI :
3.1.4.1 DESCRIZIONE DELLA FASE "FILATURA"
La filatura e l'ultima fase di lavorazione del processo. In questo reparto arrivano le "ciambelle" di stoppini, provenienti dalla cardatura, sui quali vengono eseguite le operazioni di stiro, torsione e raccolta in fusi del filato.
Il macchinario per compiere tali operazioni è costituito da filatoi intermittenti (self-acting o filanda) oppure da filatoi continui ad anello (ring); poiché le fibre utilizzate nella produzione di cardato della zona pratese sono per lo più fibre corte, la filatura viene effettuata prevalentemente per mezzo del self-acting.
3.1.4.2 ATTREZZATURE E MACCHINE UTILIZZATE NELLA FASE "FILATURA"
- Filatoio discontinuo (detto anche intermittente o filanda o self-acting): E' composto da un banco fisso dove sono posti i subbi con le ciambelle provenienti dal reparto cardatura, da un carro mobile che porta i fusi su cui si avvolge il filato e che compie i movimenti di allontanamento ed avvicinamento al banco fisso e da un castello centrale dove si trovano i motori e gli organi di trasmissione del moto. Sono state più recentemente introdotte macchine in cui anche il carro che porta i subbi esegue una parziale corsa di avvicinamento e allontanamento in contrapposizione all'altro carro.
- Filatoio continuo ad anello (ring): In questa macchina le operazioni di stiro, torsione e avvolgimento a cui è sottoposto lo stoppino avvengono contemporaneamente, in maniera continua. E' usato per titoli grossi per i quali consente una produttività maggiore che con il self-acting.
Il numero di fusi che può contenere, per il ciclo del cardato, varia normalmente da 400 a 600.
Tutti gli organi di comando sono raggruppati in una estremità (testata).
La zona di stiro è costituita da cilindri scanalati e da manicotti ruotanti che affinano lo stoppino.
Un sistema di aspirazione pneumatico con bocchette poste al disotto dei cilindri scanalati provvede a risucchiare la polvere ed i fili che si rompono.
La torsione, data al filo per aumentare la coesione delle fibre, è ottenuta da un cursore trascinato dal filo su di un apposito anello.
Il supporto che porta l'anello è dotato di un movimento di saliscendi allo scopo di formare il corpo cilindrico delle bobine di filato. I fronti di lavoro dei filatoi si trovano contrapposti due a due.
Il caricamento delle ciambelle e lo scarico dei fusi può avvenire manualmente oppure automaticamente.
3.1.4.3 FATTORI DI RISCHIO NELLA FASE "FILATURA"
Il rischio da infortuni in questo reparto è inferiore a quello presente nei reparti di preparazione e di cardatura.
Sono invece maggiori i rischi da polveri, da microclima alterato e soprattutto rumore.
- Esposizione a rumore:
- Filatoio discontinuo (self-acting):
I modelli vecchi erano maggiormente rumorosi prevalentemente a causa del dispositivo meccanico di inversione del moto del carro mobile. Valori misurati: (86 – 91 dBA.
- Filatoio continuo (ring):
Il rumore prodotto dalle macchine è sicuramente la fonte di rischio maggiore per gli operatori, esso supera in molti casi i limiti stabiliti dalle norme di prevenzione. E' dovuto principalmente alla elevata velocità di rotazione dei fusi ed al loro non perfetto bilanciamento per la bobina che si forma, alla resistenza dell'aria che il filo stesso incontra durante il suo avvolgimento ed al sistema pneumatico di aspirazione. Valori misurati: 93,5 – 97 dBA.
3.1.4.3.2 Esposizione a polveri di fibre tessili, che si diffondono nell’ambiente di lavoro.
3.1.4.3.3 Esposizione a microclima sfavorevole: Umidità e temperatura generalmente più elevate della norma, per esigenze di lavorazione delle fibre tessili.
3.1.4.3.4 Lavoro in prossimità di organi meccanici in movimento, costituiti da:
3.1.4.3.4.1 Filatoio discontinuo. Le parti più pericolose sono le seguenti:
- le ruote del carro mobile, che possono passare sopra i piedi degli addetti oppure possono essere causa di presa tra i raggi.
- la zona di battuta tra il carro mobile ed il tampone di arresto dove esiste il rischio di schiacciamento degli arti inferiori.
- gli organi di trasmissione del moto che possono essere causa di presa e trascinamento.
- la zona tra il nasello e la controbacchetta dove esiste il rischio di cesoiamento delle mani.
- lo spazio tra il banco fisso ed il carro mobile.
3.1.4.3.4.2 Filatoio continuo. Le parti più pericolose sono le seguenti:
- gli organi di trasmissione del moto che possono essere causa di presa e trascinamento.
- cilindri in rotazione nella fase di stiro dove, in caso di rottura del filo o per un difetto di aspirazione si può avere una fasciatura dell'ultimo cilindro per cui deve essere eseguita la sfasciatura tagliando con un coltello questo manicotto di filo formatosi. Questa operazione espone al pericolo di presa da parte dei piccoli cilindri in rotazione e di ferite da taglio.
- il sistema di stiro che può essere causa di impigliamento e presa dei capelli, specie in presenza di personale con i capelli lunghi
- Uso di attrezzature manuali, quali il coltello utilizzato per la sfasciatura dell’ultimo cilindro di stiro.
- Movimentazione manuale dei carichi durante le operazioni di carico delle ciambelle di stoppini, di scarico delle bobine di filato e di alimentazione dei fusi in caso di sistemi non automatizzati. Il rischio è aggravato dal fatto che le suddette operazioni vengono effettuate in posizioni non ergonomiche.
3.1.4.4 DANNI NELLA FASE "FILATURA"
- Danni uditivi e disturbi extra uditivi derivanti dall’esposizione a rumore. In relazione ai livelli di esposizione presenti in questa fase. Inoltre lo stress derivante dall’esposizione a rumore può essere causa di una maggiore esposizione al rischio di infortuni.
- Danni all’apparato respiratorio, dovuto all’esposizione a polveri di fibre tessili, per effetto dell’esposizione a microclima alterato per umidità e temperatura più elevate della norma e alla presenza dell’impianto di condizionamento dell’aria.
- Lesioni dovute ad infortuni, costituite da:
- Ferite e contusioni, per presa e trascinamento dagli organi meccanici in movimento.
- Cesoiamento delle mani, tra il naselo e la controbacchetta.
- Ferite da taglio, durante l’uso manuale del coltello per la sfasciatura.
- Ferite al cuoio capelluto per presa e trascinamento dei capelli dal sistema di stiro.
- Danni all’apparato muscolo scheletrico, derivanti dalla movimentazione manuale dei carichi in caso di sistemi non automatizzati. Il danno è maggiormente probabile perché il lavoro viene svolto in posizioni non ergonomiche.
3.1.4.5 INTERVENTI ADOTTATI PER ELIMINARE/RIDURRE IL RISCHIO NELLA FASE "FILATURA"
- Per ridurre l’esposizione al rumore degli addetti nel reparto filatura, è necessario innanzi tutto cercare di ridurre il rumore alla fonte. Sono state effettuate ricerche per la riduzione del rumore, come ad esempio l'introduzione di fusi ruotanti su cuscinetti oscillanti, che però non hanno trovato ampia diffusione.
3.1.4.5.1.1 Filatoio discontinuo: sostituzione della macchina con un modello meno rumoroso.
- Filatoio continuo: interventi sul numero dei giri e sul bilanciamento dei fusi.
L'innovazione tecnologica, con l'introduzione dei sistemi automatici di carico delle ciambelle di stoppini, di scarico delle bobine di filato e di alimentazione dei fusi, oltre a ridurre la fatica fisica degli operatori, che veniva esplicata anche in condizioni ergonomiche non ideali, consente una minore presenza degli operatori nelle zone rumorose.
Qualora i suddetti accorgimenti non risultino sufficienti ad abbattere il rumore al di sotto dei limiti pericolosi indicati dalla normativa vigente, in attesa di interventi tecnologici più efficaci, è necessario:
- Informare i lavoratori sui rischi e sui danni derivanti dall’esposizione a rumore.
- Segnalare le zone ad eccessiva rumorosità.
- Utilizzare Dispositivi di Protezione Individuali per la protezione dell’udito.
- Formare i lavoratori al corretto utilizzo dei D.P.I.
3.1.4.5.2 Per ridurre l’esposizione alle polveri di fibre tessili, è necessario un adeguato impianto di captazione e aspirazione.
3.1.4.5.3 Per ridurre l’esposizione a microclima sfavorevole, è necessario un adeguato controllo dell’impianto di condizionamento dell’aria e dei relativi valori microclimatici in modo da evitare che siano alterati in misura maggiore di quanto sufficiente per esigenze di produzione. L’impianto deve essere sottoposto a manutenzione periodica.
- L’introduzione dei sistemi automatici di carico delle ciambelle di stoppini, di scarico delle bobine di filato e di alimentazione dei fusi, consente di ridurre le occasioni di movimentazione manuale dei carichi, oltre che, come già detto, di ridurre la permanenza degli addetti in zone rumorose.
- Per eliminare o ridurre i rischi derivanti dal lavoro in prossimità di organi meccanici in movimento, è necessario:
3.1.4.5.5.1 Filatoio discontinuo:
- Le ruote del carro mobile devono essere dotate di dispositivo scansa piede.
- Nella zona di battuta tra il carro mobile ed il tampone di arresto, devono essere predisposti dispositivi quali tamponi retrattili o equivalenti.
- Gli organi di trasmissione del moto devono essere adeguatamente protetti.
- La zona tra il nasello e la controbacchetta deve essere dotata di custodia cilindrica.
- Nello spazio tra il banco fisso ed il carro mobile deve essere interdetto l'accesso quando la macchina è in moto.
- Installazione di reti metalliche o altri sistemi di sbarramento a protezione delle fiancate laterali lungo tutto lo spazio di corsa del carro.
- Installazione di un corrimano di sbarramento ai lati del castello.
- Accecatura delle ruote raggiate del carro mobile.
- Allontanamento tra di loro dei bracci di sostegno della bacchetta e contro bacchetta.
- Allargamento del vano di appoggio del settore ove esistente.
3.1.4.5.5.2 Filatoio continuo:
- Gli organi di trasmissione del moto devono essere protetti tramite un dispositivo di blocco sullo sportello della testata dove sono installati.
- Durante la sfasciatura dell’ultimo cilindro di stiro, è necessario fermare il cilindro ed il manicotto su cui si deve operare.
- Le lavoratrici con i capelli lunghi devono indossare cuffie per la protezione dei capelli.
- Per ridurre i rischi derivanti dall’utilizzo di attrezzature manuali taglienti, durante la sfasciatura dell’ultimo cilindro di stiro, è necessario:
- Usare guanti rinforzati.
- Usare coltello di sicurezza a lama retrattile.
- Formare i lavoratori a tagliare i fili che fasciano il cilindro di stiro tenendo il coltello con entrambe le mani.
- Dopo l’uso riporre il coltello in apposita tasca rinforzata.
3.1.4.6 INDICAZIONE DI EVENTUALE APPALTO A DITTA ESTERNA PER LA FASE "FILATURA"
Questa fase non viene appaltata.
3.1.4.7 RIFERIMENTI LEGISLATIVI E NORME TECNICHE PER LA FASE "FILATURA"
- D.P.R. 547/55
- D.Lgs. 277/’91
- D.P.R. 303 / ‘56
- Norma UNI EN ISO 11111 del Luglio 1997
3.1.4.8 IMPATTO ESTERNO della fase "FILATURA"
Emissioni in atmosfera di polveri delle fibre tessili in lavorazione: non esistono emissioni significative.
Diffusione di rumore nell’ambiente circostante: Il reparto filatura è il più esteso dello stabilimento produttivo e pertanto è anche quello che determina il maggior impatto di rumore sull’esterno. Nel rumore generato dalle filande sono generalmente presenti anche componenti impulsive che penalizzano i valori del rumore misurato. Tali componenti impulsive sono dovute ai battiti delle filande a fine corsa. Nel 1997 sono pervenuti all’ARPAT di Prato 3 esposti dei quali: 1 per rumore diurno il quale però rientrava nei limiti di Legge, 1 per rumore notturno che è risultato superiore dei limiti ad all’ordinanza successiva di adeguamento la ditta ha ottemperato cessando la lavorazione durante la notte e il terzo caso è in corso di esame. Si noti come nella realtà Pratese il numero degli esposti rispetto al numero delle aziende è molto contenuto anche per il fatto che il settore della filatura del cardato sta attraversando un periodo di crisi ed i nuovi stabilimenti produttivi riguardano per lo più filature a pettine i quali vengono ubicati in zone industriali. Più in generale i problemi di rumore esterno nella zona pratese riguardano maggiormente altre tipologie di lavorazione tessile, in particolare tessiture e rifinizioni di tessuti.
Produzione di rifiuti: La peluria residua del processo è stata fino ad oggi recuperata di norma o all’interno del processo stesso, o come materiale quotato in Borsa o come materiale destinato al riutilizzo. Prima del Decreto "Ronchi" tali materiali non erano soggetti a registrazione o a denuncia (M.U.D.) e pertanto non è possibile quantificarne la produzione. I quantitativi minimi di rifiuti non riutilizzati di questo processo sono stati nella maggior parte dei casi equiparati ai rifiuti urbani e smaltiti tramite l’azienda mucipalizzata.